1. Raw material preparation
First of all, make sure that the LDPE and HDPE raw materials used are of high quality and free of impurities. This requires strict quality inspection of raw materials, including detection of key indicators such as molecular weight, melt index, density, etc. Only raw materials that meet the requirements can be used for mixing preparation.
2. Determine the mixing ratio
Considerations: There are differences in physical properties between LDPE and HDPE. LDPE has better flexibility and ductility, while HDPE has higher hardness and strength. Therefore, when determining the mix ratio, there are trade-offs based on the physical performance requirements of the final product. The chemical stabilities of the two types of polyethylene also differ. HDPE generally has better chemical stability, while LDPE may be more susceptible to degradation in certain chemical environments. Therefore, in application scenarios where chemical stability needs to be considered, the proportion of HDPE should be appropriately increased. The processing properties of mixtures have an important impact on production efficiency and product quality. The melting temperature, melt index and other parameters of different proportions of LDPE and HDPE mixtures will be different, which will affect the stability and efficiency of extrusion, injection molding and other processing processes. There may be differences in the market prices of LDPE and HDPE, so when determining the mixing ratio, cost factors also need to be considered to reduce costs as much as possible while meeting performance requirements.
Determination method: Find the optimal mixing ratio by preparing mixtures of LDPE and HDPE in different proportions and testing their physical properties, chemical stability, processing performance and other indicators. Although this method is more cumbersome, it can directly obtain actual performance data and provide a strong basis for determining the mixing ratio. According to the physical properties, chemical properties and other parameters of LDPE and HDPE, the performance of the mixture under different mixing ratios is predicted through theoretical calculation. This method is relatively simple, but the calculation results may be affected by a variety of factors and need to be adjusted based on the actual situation. Based on past experience and the mixing ratio of similar products, the mixing ratio of LDPE and HDPE was initially determined and verified and adjusted in subsequent tests. This method is suitable for situations where similar products already exist and can save time and cost.
3. Mixing process selection
The choice of mixing process also has an important impact on the performance of the mixture. Common mixing processes include melt mixing, solution mixing and mechanical mixing. Melt mixing is to heat LDPE and HDPE to a molten state and then mix them. This method is simple to operate, but attention needs to be paid to controlling the mixing temperature and time to avoid thermal degradation. Solution mixing is to dissolve two polyethylenes in a common solvent and then mix them, and then remove the solvent through evaporation or precipitation. This method can obtain a more uniform mixture, but the operation is more complicated. Mechanical mixing uses mechanical force to mix two polyethylenes together and is suitable for small-scale production or laboratory research.
4. Mixing process control
During the mixing process, parameters such as mixing temperature, mixing speed and mixing time need to be strictly controlled. Too high a mixing temperature may cause thermal degradation of polyethylene and affect the performance of the mixture; too fast a mixing speed may result in an uneven mixture; too long a mixing time may increase production costs. Therefore, appropriate mixing parameters need to be selected based on the specific mixing process and raw material characteristics.
5. Post-processing and performance optimization
Once mixing is complete, the mixture also needs to be post-processed to optimize its properties. This may include steps such as cooling, granulation, drying, etc. During the cooling process, the cooling rate needs to be controlled to avoid the generation of internal stress; the granulation process needs to ensure uniform particle size to facilitate subsequent processing; the drying process needs to remove residual moisture or solvent in the mixture to prevent it from being generated during use adverse effects. To further improve the performance of the mixture, you may also consider adding some modifiers or additives. For example, antioxidants can be added to improve the antioxidant properties of the mixture; plasticizers can be added to improve its flexibility; fillers can be added to reduce costs, etc. The types and amounts of these additives need to be determined based on specific application requirements.
6. Performance testing and evaluation
Performance testing and evaluation of the prepared LDPE and HDPE mixtures are required. This includes testing its mechanical properties (such as tensile strength, elongation at break, etc.), thermal properties (such as thermal stability, melting temperature, etc.), and processing properties. By comparing the performance data of mixtures obtained under different mixing ratios and process conditions, the optimal preparation scheme can be found.
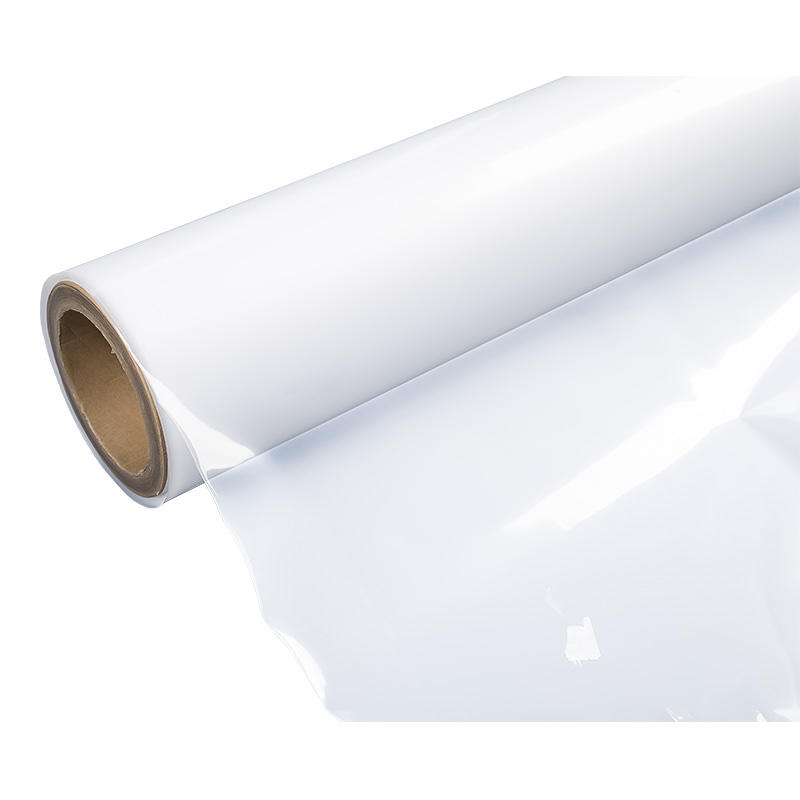