1. Overview of production process
Raw material preparation: The raw materials used to produce Soy Milk Bag CPP/PE Film mainly include CPP (cast polypropylene) and PE (polyethylene) particles. These raw materials need to undergo strict screening and quality control to ensure the purity and stability of the raw materials. Subsequently, the raw materials are mixed according to the predetermined formula ratio to prepare for subsequent production.
Melt extrusion: The mixed raw materials are fed into the melt extruder. In the extruder, the raw materials are heated to high temperatures and gradually melt into a viscous liquid state. During this process, parameters such as temperature, pressure and speed need to be precisely controlled to ensure uniform melting of raw materials and provide suitable molten materials for subsequent molding.
Calendering: After the molten material comes out of the extruder, it enters the calender for shaping. The calender is composed of multiple rollers. By adjusting the gap and pressure between the rollers, the molten material is calendered into a film. During the calendering process, it is necessary to ensure that the film has a uniform thickness, a smooth surface, and meets predetermined physical performance requirements.
Cooling and solidification: The calendered film needs to be cooled and solidified to stabilize its structure and performance. The cooling method can be air cooling or water cooling, which is selected according to production needs and product characteristics. By cooling, the molecular chains in the film are fixed, improving its mechanical properties and stability.
Coiling and cutting: After cooling and solidification, the film is continuously rolled up to form a large roll of film product. Subsequently, according to the product specifications and size requirements, the film is cut using a cutting machine to obtain the Soy Milk Bag CPP/PE Film that meets the requirements.
Quality inspection and packaging: Carry out quality inspection on the cut film, including inspection of thickness, strength, appearance, etc. After ensuring that the product meets quality standards, it is packaged and labeled and prepared for shipment from the factory. During the entire production process, the production environment needs to be strictly controlled to ensure the cleanliness and hygiene of the production workshop. At the same time, equipment maintenance and upkeep are strengthened to ensure the normal operation and stability of production equipment.
2. The importance of thickness control
Thickness is an important parameter for the performance of Soy Milk Bag CPP/PE Film. A film that is too thin may not be able to withstand the pressure of the packaging contents, causing rupture or leakage; while a film that is too thick will cause a waste of raw materials and increase production costs. Therefore, reasonable thickness control is the key to achieving a balance between product strength and cost-effectiveness.
3. Thickness control strategy
Raw material selection and proportioning
Select high-quality CPP and PE particles and proportion them according to product performance requirements. Different proportions of CPP and PE particles will affect the mechanical properties and cost of the film. By optimizing the ratio, raw material costs can be reduced while ensuring strength.
Melt extrusion process control
During the melt extrusion process, parameters such as temperature, pressure, and speed of the extruder are strictly controlled to ensure that the molten material flows out evenly and stably. By adjusting the parameters of the extruder, precise control of the film thickness can be achieved.
Calendering process optimization
Calendering is a key step in controlling film thickness. Precise adjustment of film thickness can be achieved by adjusting parameters such as roller gap, pressure and speed of the calender. At the same time, optimizing the calendering process can also improve the uniformity and surface quality of the film.
Online thickness monitoring and feedback
Install thickness monitoring equipment on the production line to monitor film thickness changes in real time. Once the thickness deviates from the set value, the relevant process parameters are immediately adjusted through the feedback system to ensure that the film thickness is always within a reasonable range.
4. Balance between cost and intensity
In the process of controlling thickness, a balance between cost and strength needs to be considered. On the one hand, by optimizing the raw material ratio and process parameters, raw material consumption and energy consumption are reduced, thereby reducing production costs; on the other hand, it is ensured that the thickness of the film meets packaging requirements and avoids quality problems caused by insufficient strength. In actual operation, the thickness and strength requirements of the film can be flexibly adjusted according to market demand and product positioning to achieve the best economic benefits.
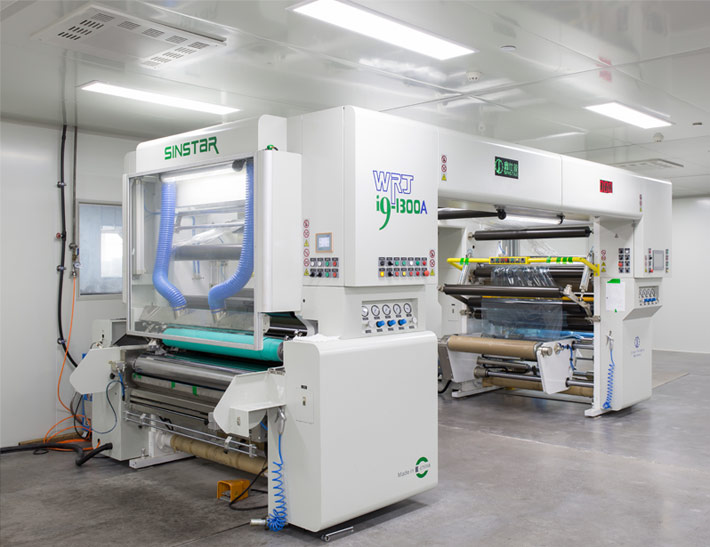